Technology
Cobra changes the game with the first commercially available 3D printed irons
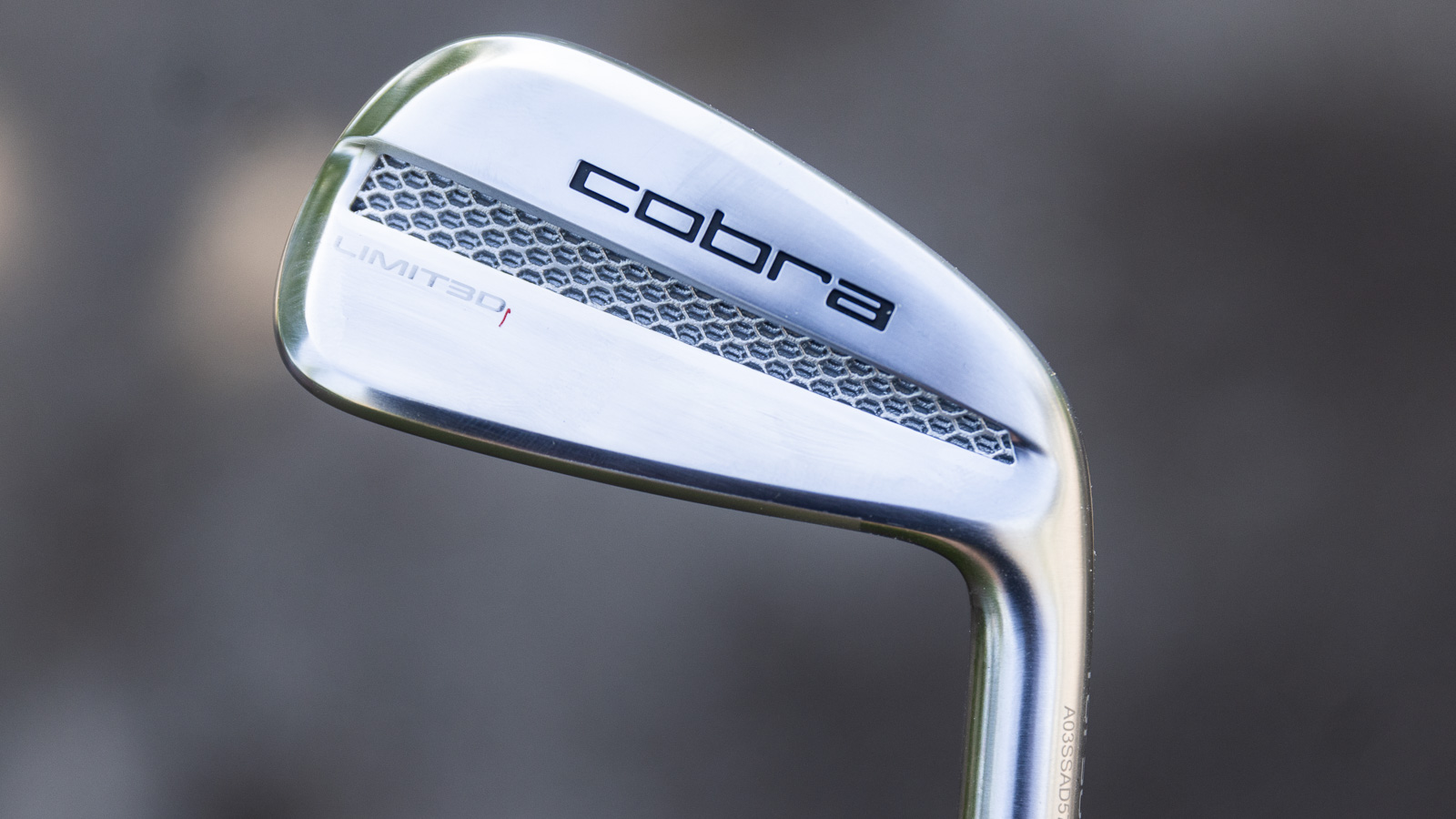
Cobra has been printing one-off golf clubs in 3D for years. Some of them are intended for testing, while others have found their way into the bags of professionals for major tournaments. But the 3D printing process has always been too slow and impractical for real commercial products that need to exist in large numbers. Now, however, the company has introduced the first-ever set of commercially available (albeit very limited edition) 3D printed irons that it calls LIMIT3D. We got a behind-the-scenes look at its development and the chance to swing a 3D printed 7-iron.
Why 3D print a golf club?
Reach your hand in any professional golfer’s bag and you’ll likely find a blade-style forged iron. These clubs have a very classic head shape with a predominantly solid back and a slim profile. They are in stark contrast to the oversized, perimeter-weighted, hollow clubs at the big box store, which are designed to help average players compensate for their relative lack of skill. Without all these tools, elite blade players can shape the shot by manipulating the clubface at impact. Place a typical knife in the hands of a beginner or even an amateur, and expect to see balls scattered across the range and probably some sore hands the next day.
By 3D printing the entire head of each LIMIT3D iron, Cobra can place the head weight virtually anywhere it wants. This provides a lower center of gravity and heavier weight distribution to get the ball into the air easily and keep it flying relatively straight.
What are they made of?

The entire head of the iron is 3D printed from 316L stainless steel. Unlike forged iron, which consists of solid or hollow metal, LIMIT3D irons contain a metal lattice structure based on repeating dodecahedral structures. The grille is visible at the back of the club head, but that is purely aesthetic and not tied to the actual structure of the club.
The LIMIT3D irons are almost the same size as Cobra’s King Tour iron, but the two feel very different upon impact. The 3D printed iron grid cuts a whopping 100 grams of weight from the center of the club head, compared to its forged counterparts. To maintain consistent performance, Cobra adds those 100 grams back in the form of welded-in weights at the toe and hosel. That weight helps prevent the club from spinning at impact, a common problem among lower-level players that often sends the ball into the parking lot instead of the hole. The lowered center of gravity also helps get the ball in the air to create more distance along a good flight path. The LIMIT3D is a true blade-style iron that offers many of the same features found in so-called ‘game improvement’ irons designed to assist higher handicap players.
How do you print a golf club in 3D?

Cobra uses a process called direct metal laser sintering (DMLS) to build the LIMIT3D clubs. This process involves making approximately 2,600 stacked layers of a fine raw material powder. The process does not require any support like a typical plastic 3D printer. The metal print creates the lattice structure in the head of each golf club. Because the grille contacts both the back of the club and the face of the club, that internal structure makes the face almost as stiff as a solid or hollow forged club. Cobra also claims that this makes the 3D printed clubs just as durable as their counterfeit counterparts.
Cobra has used this process repeatedly over the years for one-off projects. Some of the 3D printed clubs have even found their way into professional touring bags. But producing them on a large scale can be pricey and time-consuming. While the $3,000 price tag for the limited edition sets sounds high, Cobra suggests that a set like this could have cost ten times as much, or even more, a decade ago.
It takes about 24 hours to print an iron head tray from bottom to top. Then Cobra welds in the tungsten weights, grinds the face, polishes the head and laser-etches the branding. There is no heat treatment involved.
Cobra claims that this DMLS process is the only method that can create such a delicate internal lattice. Other commonly used metal 3D printing techniques, such as Metal Jet or Binder Jet, cannot achieve this shape or meet the tight tolerances.
How does it feel to hit the LIMIT3D 3D printed clubs?

Cobra provided me with a steel 7-iron to try out. My skills landed me firmly in the game improvement end of the market, especially after an injury a few years ago that drastically changed my swing.
Looking down on the club is strange. I’m used to playing more oversized irons with a noticeable offset, meaning the clubface sits back from the shaft to promote a square clubface at impact. Consumer-oriented clubs have a much coarser top line and overall shape. However, the LIMIT3D clubs look like a real frame with a relatively thin top line. There are a lot of golfers who love the look and even the idea of playing with forged blades, but they (we?) just don’t have the skill for it. That’s exactly who Cobra is targeting with the LIMIT3D series, and presumably all future clubs that will rely on this manufacturing process as it becomes more scalable.
I only took a few cuts before my neck started telling me my time at the range was up. Still, I was surprised by the feeling. I’ve hit with blades in the past and if I didn’t hook the ball properly, I couldn’t get it on an optimal trajectory, at least not with any regularity. The LIMIT3D club definitely gave me a better launch angle and tamed my hook into a more controllable draw, just as I would expect from a game improvement iron. I still managed to hit a few off the tungsten-weighted toe of the bat, but those bad shots didn’t sting my hands like they would with a knife.
Cobra claims the redesigned head leads to higher ball speed at launch compared to similar typical blades. That could mean up to five additional yards of distance, which is a significant jump over an entire set of irons.
Can you get a set of LIMIT3D irons?
At this time, Cobra is only releasing a total of 500 sets of these 3D printed irons worldwide. They are right-handed only and the kit includes 4-PW for a price of $3,000. That’s obviously a hefty premium over a standard set of high-end knives (which typically range between $1,000 and $1,500), but they are a collector’s item. Cobra hasn’t publicly announced plans for a wider release, but this 3D printing process is clearly making waves throughout the industry and we’re only just beginning to see what’s possible.